Tensegrity, a simple example, and uses in Industry

Tensegrity is a structural principle that combines tension and integrity, or as Buckminster Fuller, who coined the term, put it: “islands of compression in an ocean of tension”. Tensegrity structures are composed of isolated components under compression (such as rods or struts) that are held together by a network of continuous tension (such as cables or tendons). The key feature of tensegrity structures is that the compressed members do not touch each other, while the tensioned members define the shape and stability of the system.
Tensegrity structures have some remarkable properties that make them attractive for various applications. Some of these properties are:
- They are efficient in terms of material use and weight, since they only use compression and tension forces, avoiding bending moments and shear stresses that would require thicker members.
- They are adaptable to changing loads and environments, since they can adjust their shape and stiffness by changing the tension in the cables.
- They are resilient to damage and failure, since they can redistribute the stress among the members and maintain their integrity even if some components break.
- They are aesthetically pleasing and inspiring, since they create complex and elegant forms that challenge our perception of gravity and balance.
Tensegrity structures have been used in various fields, such as art, architecture, engineering, biology, medicine, robotics, and space exploration. Some examples of tensegrity structures are:
- The Skylon, a 90-meter tall tower that was erected for the Festival of Britain in 1951. It was supported by six cables at each end that defined its position and orientation. It was one of the first examples of a large-scale tensegrity structure.
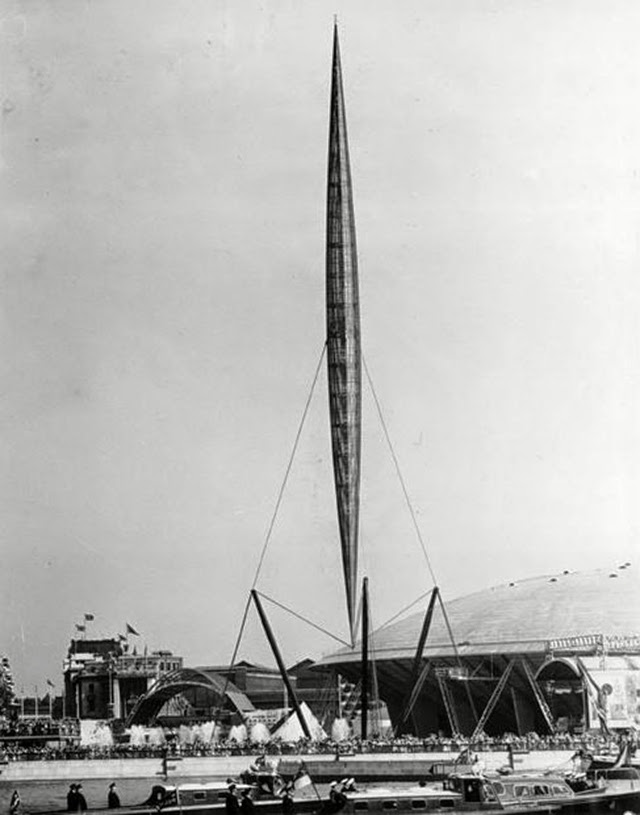
- The Needle Tower, a 18-meter high sculpture by Kenneth Snelson, who pioneered the art of tensegrity. It consists of six aluminum tubes and 24 steel wires that create a dynamic and stable form. It is displayed at the Hirshhorn Museum in Washington DC since 1968.
- The Biosphere 2, a 1.27-hectare facility that simulates different ecosystems on Earth. It was built in Arizona in 1987-1991 using a geodesic dome with a tensegrity frame. It was designed to be self-sustaining and to test the feasibility of living in space.
- The NASA Super Ball Bot, a prototype robot that can explore rough terrains on other planets. It is made of rigid rods and elastic cables that form a spherical tensegrity structure. It can change its shape and bounce to move around obstacles and absorb impacts.

As you can see, tensegrity is a fascinating and versatile concept that has many potential applications in industry and beyond. If you are interested in learning more about tensegrity, you can check out some of these resources:
- The Tensegrity Wiki (https://tensegritywiki.com/), a collaborative platform for sharing information and projects related to tensegrity.
- The International Society for Tensegrity Structures (https://www.tensegritystructures.org/), an organization that promotes research and education on tensegrity.
- The Tensegritool (https://tensegritool.com/), a software tool that allows you to design and simulate tensegrity structures.
I hope you enjoyed this blog post and learned something new about tensegrity. Thank you for reading and check out my simple homemade example below.
: https://www.merriam-webster.com/dictionary/tensegrity
: https://en.wikipedia.org/wiki/Tensegrity
: https://www.massagemag.com/biotensegrity-the-structural-basis-of-life-129777/
: https://en.wikipedia.org/wiki/Skylon_(Festival_of_Britain)
: https://en.wikipedia.org/wiki/Biosphere_2
: https://www.nasa.gov/feature/super-ball-bot
Tensegrity Simple Example
Adobe Illustrator screenshot
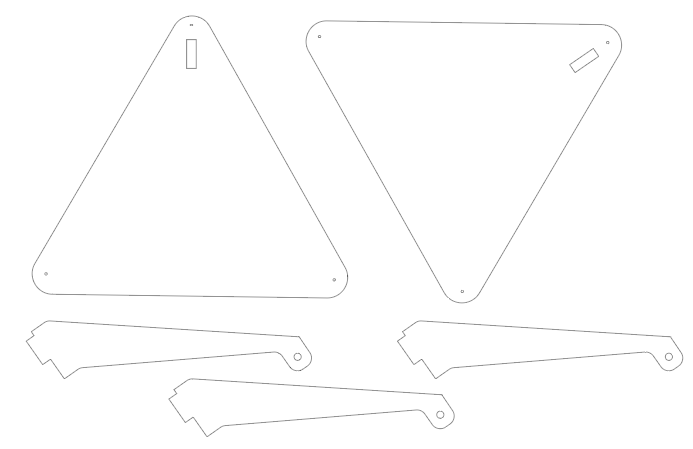
I cut these parts out of 2mm basswood using a 5w diode laser (extra arm because it fit within the scrap material I was cutting from).
Assembled, using eyehooks and fishing line and by using a bit of wood glue to join the arms to the triangle faces.
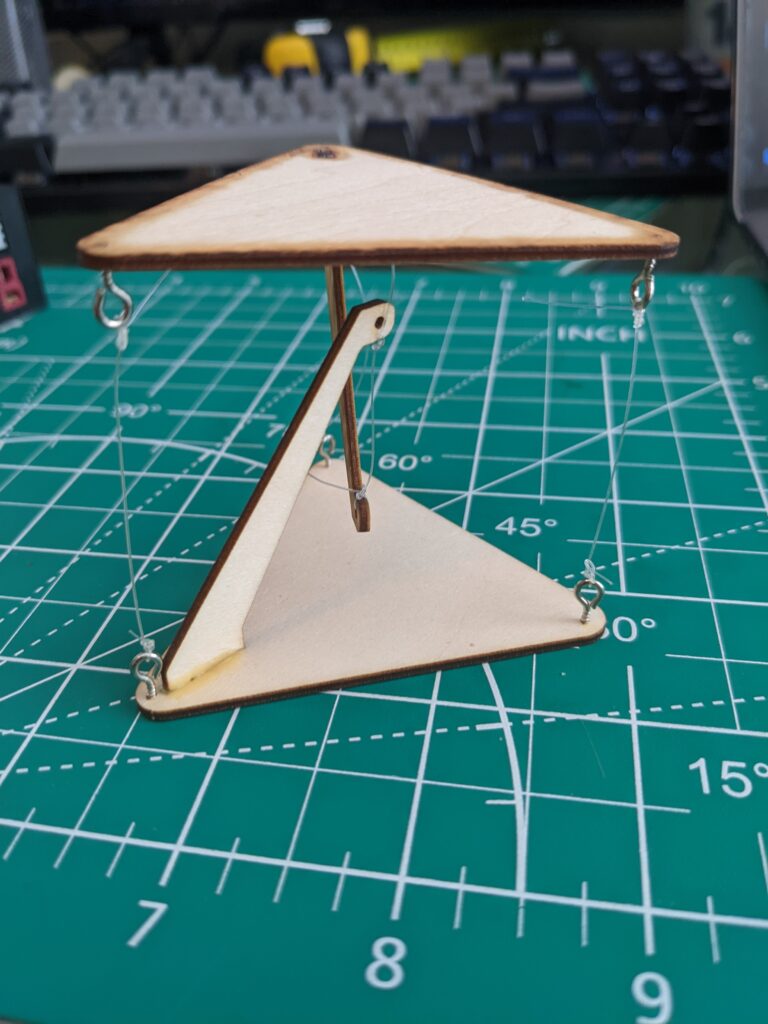
The outer three supports are only for stability — the load itself is carried entirely by the tension between the two arms perpendicular to the triangle faces.