Mounting Aileron Servos inside Wing Assembly
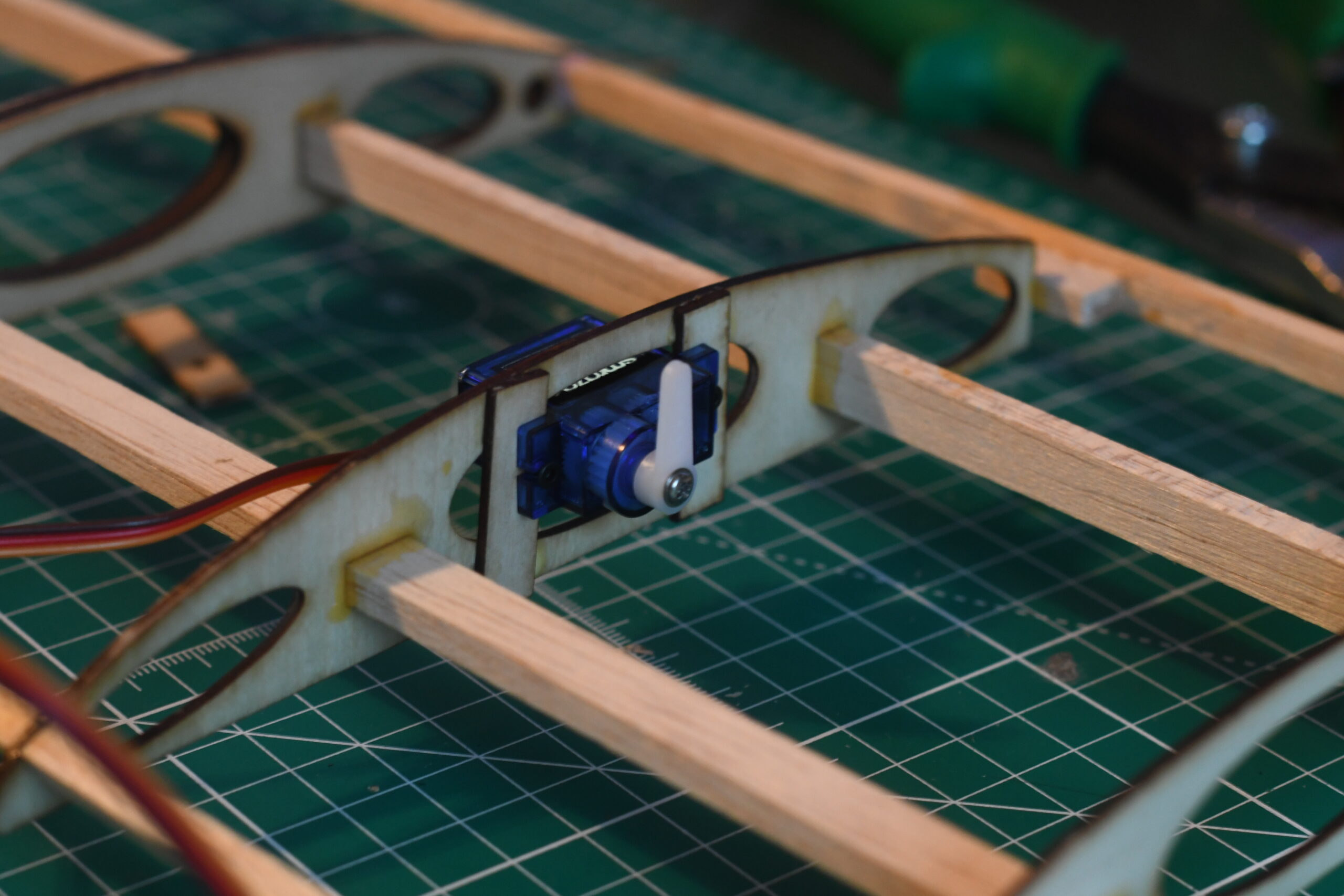
I’m currently working on a balsawood RC airplane with a 52″ wingspan. The frame of the “wing assembly” is not yet fitted with servos. The purpose of this post is to outline the design considerations taken and the matching implementation.
Existing Components
- Wing Assembly
- Aileron (2x)
- micro-servo (2x)
- control arm (2x)
- horn for control arm (2x)

(On future builds, I will consider the mounts for the servos while designing the wing cross-sections, rather than mid-way through fabrication!)
Main Problem
Need to provide stability to the servo within the wing structure to facilitate aileron control.
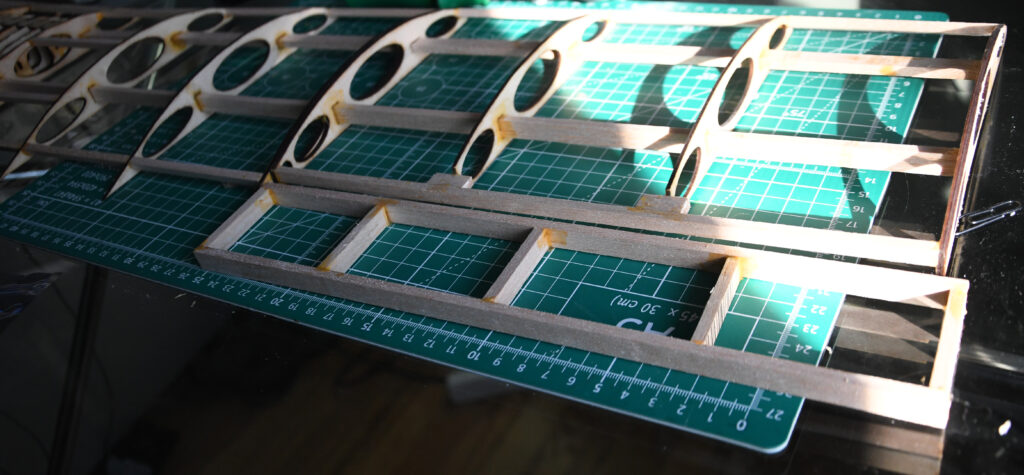
Proposed Solution
For each servo, cut two strips of 2mm plywood that will fit on either side of the servo and glue directly to the wing cross-section. There should be a hole cut into each of the trips to match the pre-cut holes in the servos mounting bracket.
3D Printing is an option, but seems overkill here. I’m also still not confident how to bond/join PLA to balsawood.
Design Needs
Need to produce drawings for the strips. Consistency is more important than precision here.
Implementation
- The first designed and cut support arm had the 2mm mount hole too far from the edge, leading to inability to use M2 bolt. I nudged it over, then re-cut
- The second designed and cut support arm fit the M2 bolts great, but would result in the servo laying too low in the wing’s profile. The mount hole needed to be nudged up a bit
- The third iteration of the support arm fit great! I used the mount nuts/bolts so that the servo was fitted at the time of gluing the support arms into the wing cross section. Supporting the extra weight of the servo is not ideal while gluing, but it was convenient to have 100% confidence that the spacing between the arms are correct
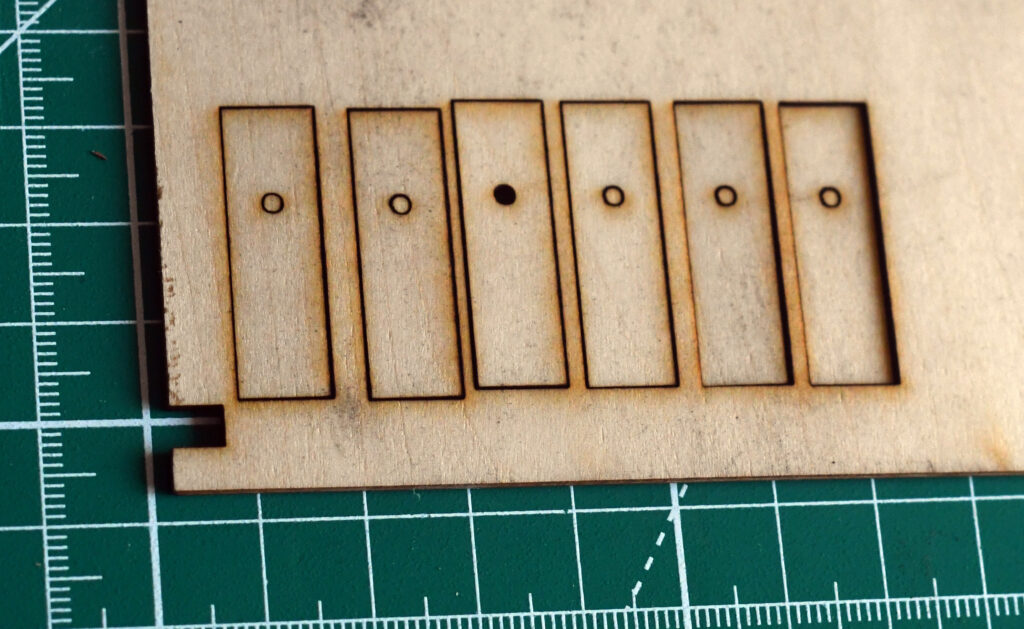

Progress Notes
- “measure four times, cut three times” – I want to set a personal goal of better measuring, planning, designing pre-fabrication to avoid as many re-dos as possible. In this post I’m designing/cutting the most simple of 2D parts, but I still cut 2 versions of a 4x part. In this case, the pieces are tiny and I was able to re-use the same piece of stock, but this could have been a much more expensive lesson
- component symmetry: based on the limited throw of servo I was planning on simply flipping the servo over to accommodate right vs left aileron. In this case, since the servo is asymmetrical on the X labelled axis, the center of the servo shafts are not equidistant from the trailing edge of the wing
